Air compressors are strong and vital appliances that make a variety of difficult activities easier. These powerful devices have proven their worth in commercial and industrial environments, which is essential for improving day-to-day operations. These articles explain how a truck air compressor works.
How a Truck Air Compressor Works
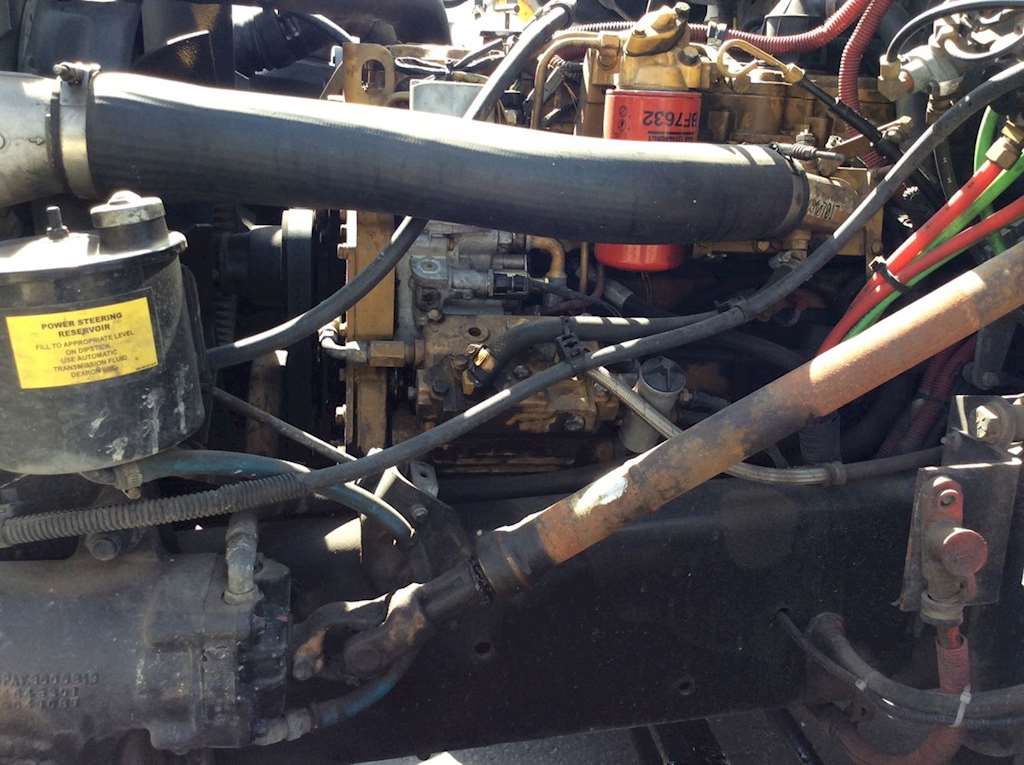
The air compressor pumps air into the aerators (tanks). The air blower is linked to the machine by gears or a V-belt. The compressor can be cooled by air or by the engine’s cooling system. It can have its oil supply, or it can be lubricated with engine oil.
Air compressors work by pushing air into a container and compressing it. The air is then expelled through an opening in the tank, where pressure is created. Think of it as an open balloon: compressed air can be used as energy when released.
The air blower produces pneumatic force for the air suspension, helper parts, and stopping mechanism. In most circumstances, the air compressor is lubricated with engine oil and cooled with engine coolant.
Depending on the compressor model, it sucks in filtered air, either straight from the truck’s air filter (at atmospheric pressure) or through the engine turbocharger, which is already under enhanced pressure. The air is then compressed until it achieves the system’s desired pressure.
A compressor is the compressed air source since it draws air from the environment and compresses it (presses). Through an air pipe, pressurized air is pushed into a storage tank. The compressor is installed on a bus or truck’s engine. All of the vehicles use piston air compressors.
Ways to keep your truck’s air compressor running smoothly
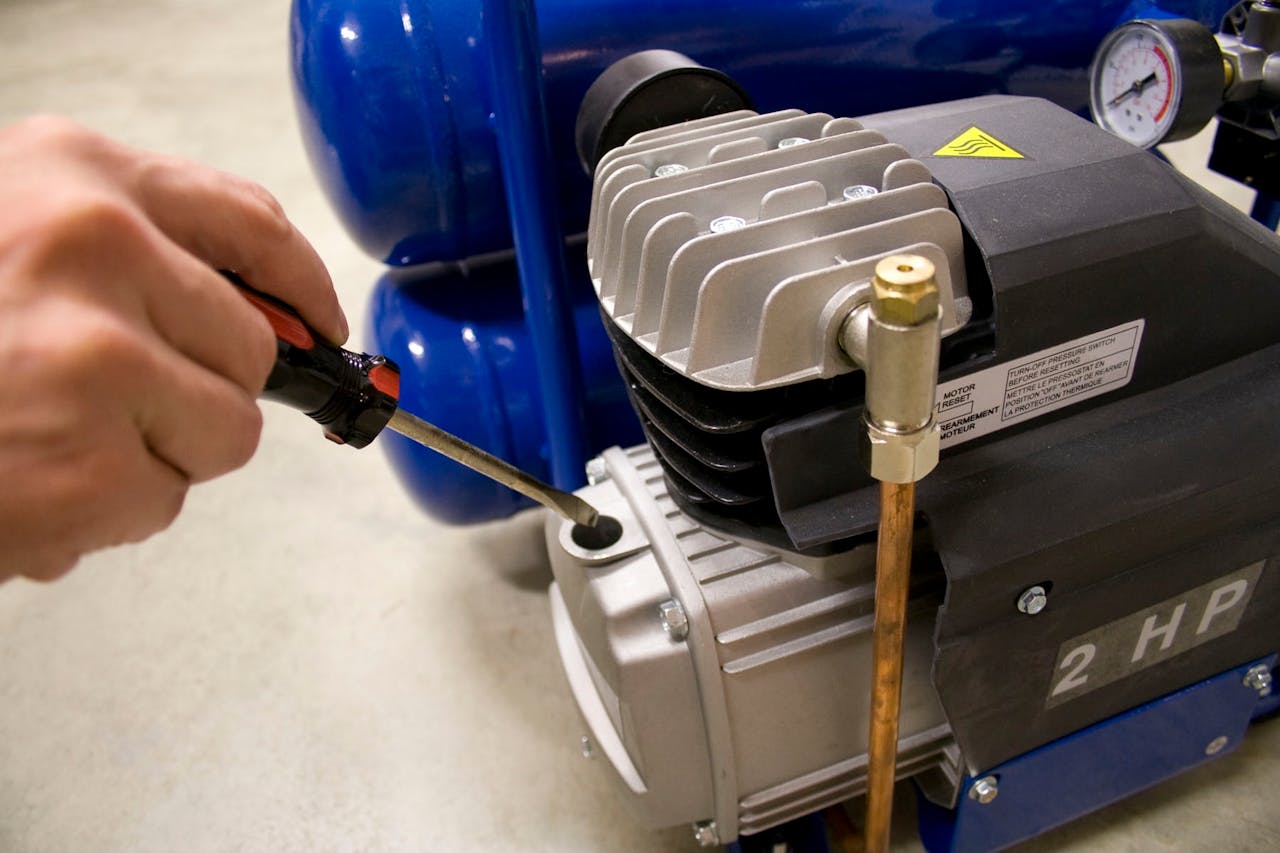
Brake function
A constant supply of compressed air is required within a predetermined maximum and minimum pressure for the braking system to work properly.
When the compressor is operating loaded, the regulator monitors the air pressure in the storage tank and controls when the compressor needs to pump air into the air system.
The compressor can fall over with no pressure in the building once enough air is in the system, known as “running no load.”
Duty cycle
The compressor duty cycle is the ratio between the time it spends generating air and the total running time of the motor. Truck air compressors generate air pressure or are “loaded” up to 25 percent of the time. Assume that the compressor has higher duty cycles, which leads to higher compressor head temperatures, which can adversely affect the performance of the air brake system.
Air System Control
The discharge pipe ensures that the mixture of air, water, and oil vapor can cool down between the compressor and the air dryer. The temperature of the air dryer input is crucial to the purity of the air system and the functioning of the air drier.
For example, when the compressed air temperature reaches the air dryer in the normal range, the dryer removes most of the oil from the filling system. Then again, the temperature of the packed air is over the typical reach; oil can go through the air dryer and very high framework as oil fumes.
Air supply
Packed air goes from the air dryer to the air tanks, or air tanks, as they are usually called. Air is normally provided to the essential stopping mechanism supply and afterward to the optional slowing mechanism repository. Once both tractor brake circuits are fully charged, air can be supplied to each tank attached to the trailer.
The air pressurizes the reservoir and air hoses to the next control valve, where the air pressure stays ready for use with each system.
Other than air suspension and braking, trucks employ compressed air for various purposes.
Normal braking
When the driver operates the foot brake, the plunger in the foot brake pedal valve moves and opens the channels in the foot brake valve allowing the air pressure waiting there to pass to the primary and secondary braking systems now, the air pressure in the brake chambers increases rapidly, with force acting on the brake rod and transferring this force to the air disc brake or through the clearance adjuster to the base drum brake.
The air from the brake chambers is swiftly discharged when the brake pedal is removed, and the brake pads or brake shoes return to their regular driving position.
Vehicle parking
Powerful springs integrated inside the spring brake are used for parking automobiles. To apply the brakes and secure the cart, the force of the spring is subdued by the application of air pressure when the driver prepares to depart and releases the parking brake, and the brake pad returns to the driving position. The anti-slip valve in the system design prevents the employment of both spring and service brakes simultaneously.
Air pressure gauges
In the early 1970s, government regulations required vehicles equipped with air brakes to have a two-circuit air system. The advantage of a double-circuit air system was that if the primary circuit failed, the vehicle could still stop with only the second separate air circuit.
Finally, regularly draining moisture from the air tanks is one of the finest methods to keep your air system in good shape.
Frequently Asked Questions
How is air compressors filled?
Every time you use a power tool, the pressure in the tank drops as compressed air passes through the hose to your tool. When the tank pressure becomes too low, the compressor restarts and refills the tank.
Will the air compressors run out of air?
There are different air pumps, each with its own unique set of benefits. There are a few things to consider when deciding which one is right for your needs. The first thing to consider is cost. There are many different air pumps, so it’s important to research the different brands and types before making a decision.
Another important factor to keep in mind is performance. What is the best pump for your particular situation? Finally, remember that a large air tank will always perform better than a small one.
What length could you run the blower?
Contingent upon the size and kind of blower, air blowers can be used from a couple of hours to 24 hours, seven days per week. Knowing your blower and its requirements and impediments is fundamental to keeping up with the appropriate working of this significant machine.
What time does it take to fully charge the air blower?
The CFM’s more noteworthy, the quicker the blower can siphon air into the tank. The more air that must be put into the tank to fill it, the larger it is. Most of the time, you’ll see that it shouldn’t take more than 2-5 minutes.
Where does the air compressor on the truck go?
The compressor may be mounted directly below the vehicle’s rear diffuser. Alternatively, the compressor may be mounted on an upper shelf of the frame rail. The compressor’s air inlet and exhaust ports are preferably located below the frame rail.
Similarly, the compressor’s air outlet and exhaust ports are preferably located below the frame rail. It is advantageous to have an air intake port located directly above the frame rail on the cabin roof.
This maximizes the amount of fresh, circulating air that the compressor can utilize. It also allows for better cooling because the fresh, circulating air is drawn directly into the compressor.
Other advantages of this mounting location include ease of installation, reduced maintenance, and fewer moving parts required to maintain high-quality performance.
Conclusion
In the same way, as other vigorously used machines, air blowers require standard support to keep up with productivity and viability. In any case, they are inclined to mileage with concentrated use. At last, you run into issues. Luckily, it doesn’t need to be costly.
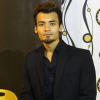